Historique ELEFIL sas
ELEFIL A votre service depuis 1984 dans le domaine de l'éléctro érosion par fil
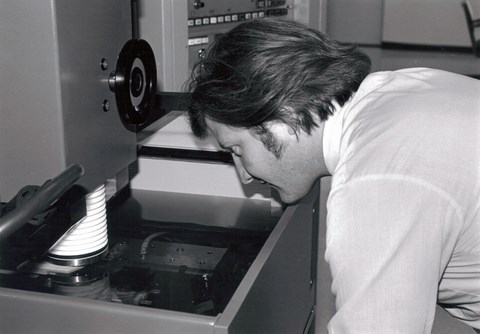
ELEFIL a été créé en 1984 par Mr DANIEL GAVARD sous forme d'une SARL au capital de 20.000 francs avec comme moyen de production une machine à fil Charmilles F40 dans un local de 16 m2. En 1987, ELEFIL se transforme en SA au capital de 250.000 francs et emménage dans un atelier neuf de 100 m2 tout en continuant à investir en matériels et personnels qualifiés. Deux ans plus tard, l'atelier est agrandi à 200 m2 et devant le succès croissant de ses activités et un certain manque de place, ELEFIL déménage en 1994 dans des locaux ultras modernes de 650 m2 spécialement conçus pour son activité.
En 1999 ELEFIL décide d'investir à l'étranger et crée ELEFIL USA, cette filiale sera revendue 2 ans plus tard. Entre-temps ELEFIL SA augmente son capital à 200.000 euros.
En 2003, elle est revendue à la SARL HOLDING ELEFIL composée de 3 employés et du fondateur. Aujourd'hui, ELEFIL SA est devenue ELEFIL SAS, elle investit massivement dans du matériel à la pointe de la technologie.
C'est au 31 mars 2009 que Daniel GAVARD prend une retraite bien méritée et laisse donc place aux 3 associés Messieurs Nicoud Pascal, Seigneur Benoit et Pellet Alain.
En septembre 2015, un 2ème site ELEFIL dédié exclusivement à la découpe en éléctro érosion de haute technicité, ouvre ses portes sur le canton de Fribourg en Suisse. Nommée ELEFIL SWISS, elle possède pusieurs machines de dernière génération Agié Charmilles Cut 1000 eau et 1000 et 2000 Oil tech pour répondre aux exigences les plus pointues en terme de découpe fil. Pour plus d'information sur cette nouvelle entité veuillez consulter le site dédié sur www.elefilswiss.com
L'aventure ELEFIL continue.....
HISTORIQUE DE L'ÉTINCELAGE PAR éLÉCTRO éROSION
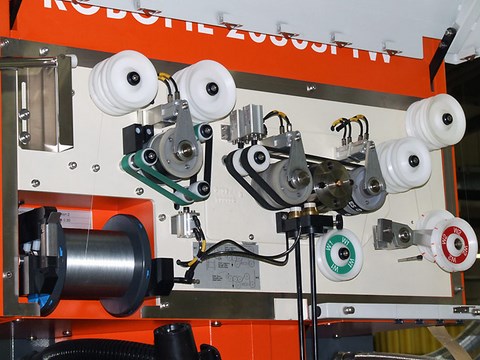
électriques. C'est en faisant des recherches pour éliminer cet effet érosif sur des contacts électriques que les savants Soviétiques B.R. et N.I. Lazarenko eurent l'idée d'exploiter l'effet destructeur d'une décharge électrique et de développer un procédé contrôlé d'usinage des métaux.
En 1943, ils mirent au point un procédé contrôlé d'usinage, appelé ainsi en raison du fait qu'une succession d'étincelles (décharges électriques) s'opère entre deux conducteurs de courant immergés dans un liquide diélectrique. Le principe du générateur de décharges utilisé alors, appelé circuit Lazarenko, a été utilisé pendant longtemps dans la construction des générateurs pour machines d'étincelage.
L'évolution spectaculaire de l'étincelage est due, également, à l'assuidité de beaucoup d'autres chercheurs qui ont contribué à mettre en lumière les caractéristiques fondamentales de cette méthode d'usinage et d'en tirer aujourd'hui les meilleurs profits.
PRINCIPE PHYSIQUE DE L'ÉLÉCTRO ÉROSION
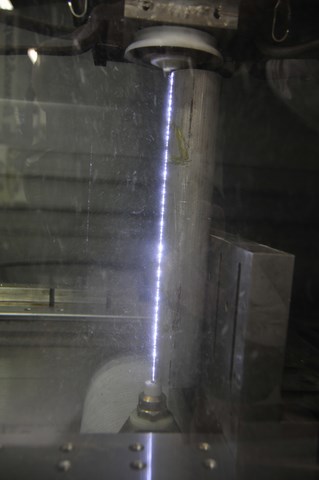
Cette tension de claquage dépend :
- de la distance entre les deux électrodes,
- du pouvoir isolant de diélectrique,
- de l'état de pollution du gap.
À l'endroit du plus fort champ électrique, une décharge va s'amorcer qui sera l'aboutissement d'un certain processus.
a) Sous l'action de ce champ, des ions libres positifs et des électrons vont se trouver accélérés,acquérir de grandes vitesses et, très rapidement, constituer un canal ionisé, donc conducteur.
b) À ce stade, le courant peut circuler et l'étincelle s'établit entre les électrodes, provoquant une infinité de collisions entre les particules.Une zone de plasma se forme.
Elle atteint rapidement de très hautes températures, de l'ordre de 8000° à 12000°C, et se développe sous l'effet de chocs toujours plus nombreux qui entraînent la fusion locale et instantanée d'une certaine quantité de matière à la surface des deux conducteurs. Dans le même temps, une bulle de gaz due à la vaporisation des électrodes et du diélectrique se développe et sa pression s'accroît régulièrement jusqu'à devenir très importante. Au moment de l'interruption du courant, le brusque abaissement de température provoque l'implosion de la bulle, engendrant des forces dynamiques qui ont pour effet de projeter la matière fondue à l'extérieur du cratère. La matière érodée se resolidifie alors dans le diélectrique sous la forme de petites sphères et elle est évacuée par ce dernier. L'érosion sur les électrodes est dissymétrique et dépend, notamment, de la polarité, de la conductibilité thermique, de la température de fusion des matériaux, de la durée et de l'intensité des décharges. Elle est appelée usure lorsqu'elle a lieu sur l'électrode. En choisissant les matériaux d'électrodes appropriés et en influençant la décharge en variant sa durée, son intensité et sa polarité, on peut arriver à une dissymétrie importante :
Par exemple, obtenir 99,5% d'érosion sur la pièce et 0,5% sur l'électrode outil.
L'électro érosion par fil utilise ce principe, ou l'électrode est un fil, connecté à un pôle, et la pièce à usiner connectée à l'autre pôle. Pour compenser l'usure pendant l'usinage sur l'électrode, le fil est en déroulement continu entre deux guides. Le tout est piloté par une commande numérique permettant à la table des déplacements du fil selon des formes programmées plus ou moins complexes suivant des axes X et Y.
Cette même commande numérique pilote également les déplacements programmés
du guide-fil supérieur suivant les axes U et V permettant l'usinage des formes inclinées
ou en dépouille.